Home/Kerr Contractors gets more done in less time with streamlined surveys
Kerr Contractors gets more done in less time with streamlined surveys
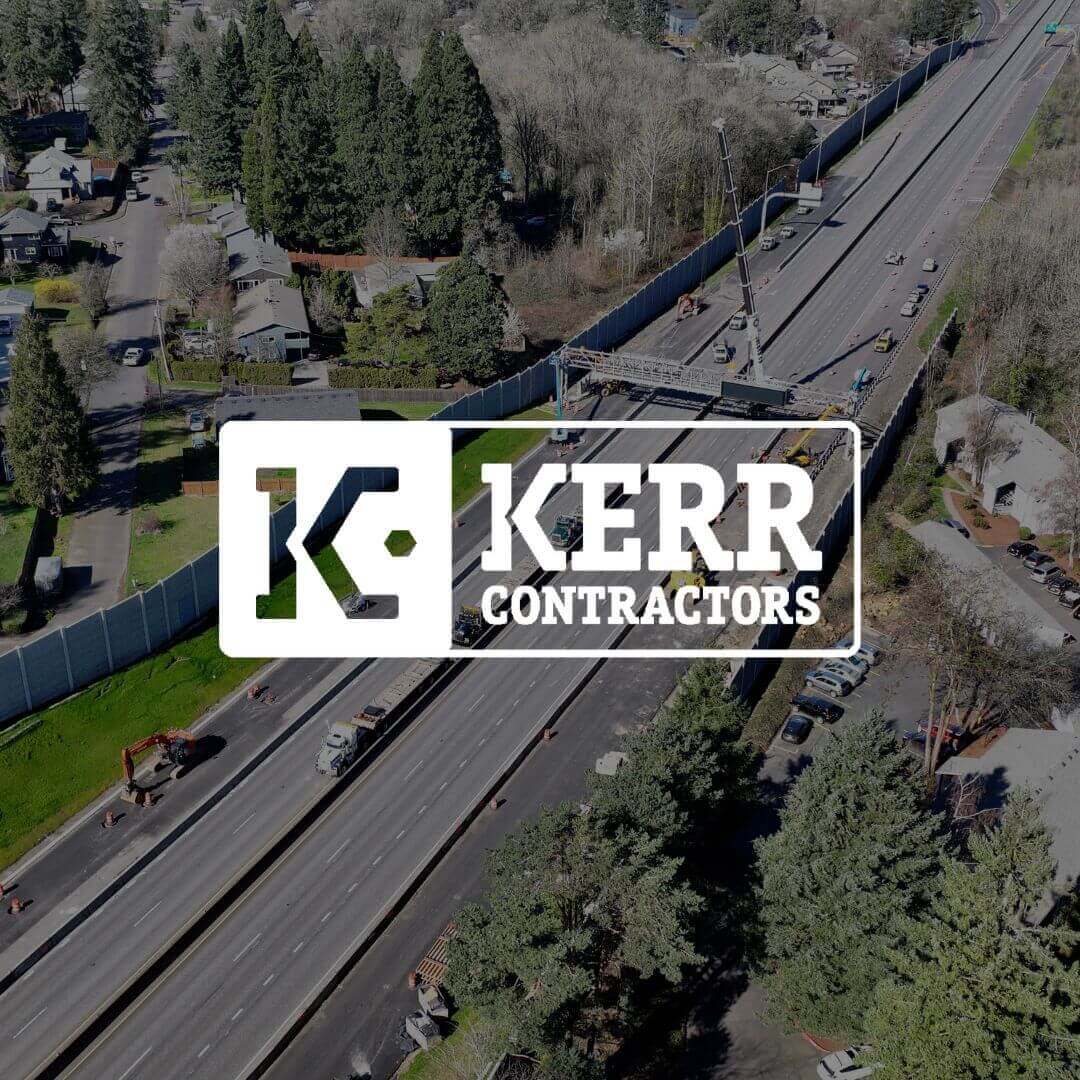
Trusted with the Pacific Northwest’s critical infrastructure for over 35 years, Kerr Contractors is a leading heavy civil general contractor and construction management firm headquartered in Woodburn, Oregon. They specialize in everything from major roadwork projects to large-scale site development and utilities, with a portfolio spanning complex projects as large as 200 acres.
Alex Hass, Kerr’s drone pilot and GPS technician, has long championed the use of cutting-edge technology to tackle challenges. Since he joined the Kerr Contractors team over a year ago, Alex has helped transform their drone surveying program into a streamlined, collaborative workflow anyone can use.
The problem: Painfully slow manual processing
When Alex joined Kerr Contractors, the team was already using drones for surveying, but they faced significant obstacles using the data. Using their old workflow, Alex soon ran into challenges:
- Painfully slow processing: Large datasets of 1600+ images could take over eight hours to process locally, tying up Alex’s laptop and often crashing before completion.
- Inefficient data-sharing: Survey data was only accessible to licensed team members, requiring lots of back-and-forth phone calls to extract usable information for project managers and superintendents.
- Limited visibility and trust: The workflow required manual adjustments and lacked reliable quality checks, which made it hard to trust the accuracy of their data outputs.
The cumulative impact of these bottlenecks was especially painful on large-scale projects, such as Kerr’s 10-mile freeway reconstruction project or multi-acre quarries requiring frequent site visits. “The process was technically ‘working,’ but it wasn’t what I hoped it would be,” said Alex.
Before Propeller, it was always just guesses. ‘It feels like it’s close’ was the most we could say. Propeller is so simple—everyone’s working off the same file in our local coordinate system, where all data can sync with our field data collectors. You can get trustworthy data very easily.” —Alex Hass, Drone Pilot and GPS Technician

The solution: Propeller’s simple and reliable workflow
Almost as soon as he tested Propeller, Alex recognized it as the ideal solution for their challenges.
Using cloud-based processing, Alex no longer has to babysit a laptop for hours. Large datasets process in the background with no manual intervention, freeing up his time for other tasks and enabling more frequent surveys.
Propeller has saved me a lot of time. I can upload the images for all four quarries at the same time on different tabs, which allows me to get the stockpile inventory data to our managers in the quickest way possible.” —Alex Hass, Drone Pilot and GPS Technician
Sharing data with the people who need it is also far easier. Propeller’s user-friendly platform empowers everyone to access the measurements they need—and see where the data came from—with no phone tag required.
And thanks to improved visibility in Propeller’s reporting, Kerr’s team can trust that they’re getting reliable, accurate data every time. Initially, they gut-checked the data from Propeller using AGTEK. “It was always spot-on,” Alex said. “That made us trust it.”

Kerr’s favorite features and workflows:
- Stockpile reporting: Alex flies Kerr’s quarries monthly to measure stockpile volumes. He then sends detailed reports to the quarry managers, who can see quantities alongside compaction rates and prices. They can also see which data Alex excluded and why, adding a layer of trust to their measurements.
- Cut-fill measurements: Kerr uses cut-fill quantities both internally and externally. Recently, they used cut-fill reporting to keep a subcontractor accountable, showing where material quantities had been distributed incorrectly and providing specifics about where work needed to be redone.
- Linework: Kerr’s project managers use Propeller daily. One project manager recently turned on linework and noticed that a manhole was missing or not adjusted. “He was able to get into Propeller directly and get the error corrected right away, rather than one of us catching it a month or more down the line,” Alex said.
- Vertical face imagery: Alex has also been tinkering with Smart Oblique surveys, which involve capturing photos at a 45-degree angle for improved vertical face imagery. Because Kerr does a lot of big building site work, they use it to show that buildings, retaining walls, and other vertical features look the way they should.

The results: Huge time savings and increased trust in drone data
Now that his time isn’t monopolized by data processing, Alex can focus on flying more often, visiting more sites, and having conversations about what the data means rather than how to deliver it.
Under the old workflow, Alex might not get data until two days after a drone flight, with an additional day and a half of manual effort to make that data usable. Now, he can process multiple surveys at once, giving project managers and supervisors direct access to the data they need as soon as the data is ready.
With Propeller, we have more communication on what the numbers actually mean, versus, ‘Here’s the numbers, I hope they’re right.’” —Alex Hass, Drone Pilot and GPS Technician
Propeller has become the go-to platform for site measurements, eliminating guesswork and shaving days from Kerr’s previous workflow, freeing the team to get more done in less time.
It’s also an asset in client meetings, where project managers regularly pull up Propeller to share updates. “If a big meeting is happening, I usually get a call to fly the day before. [Propeller] is a good tool to look professional, ensure everyone is seeing the most recent imagery, and collaborate together,” said Alex.

Want to know how Propeller can help you?
Learn more about Propeller’s products, pricing, and how to get started on your site.