The Internet of Things (IoT) has put a massive amount of information at our fingertips. Real-time access to that information is changing the way we work, and the construction industry is no exception.
According to a 2020 Gartner survey, even the disruptive impact of COVID-19 didn’t slow down IoT growth. 47% of organizations plan to increase their investments in IoT technology and implementation, and the rate of investment is only picking up.
Digital twins—or digital representations of physical objects—are one of the most accessible ways to leverage IoT for your business. Gartner predicts that by 2021, half of large industrial companies will use digital twins, and they’ll see a 10% boost in efficiency as a result.
This technology represents an exciting opportunity for earthworks, so let’s unpack what it means to create a digital twin in construction and how it can improve your operations.
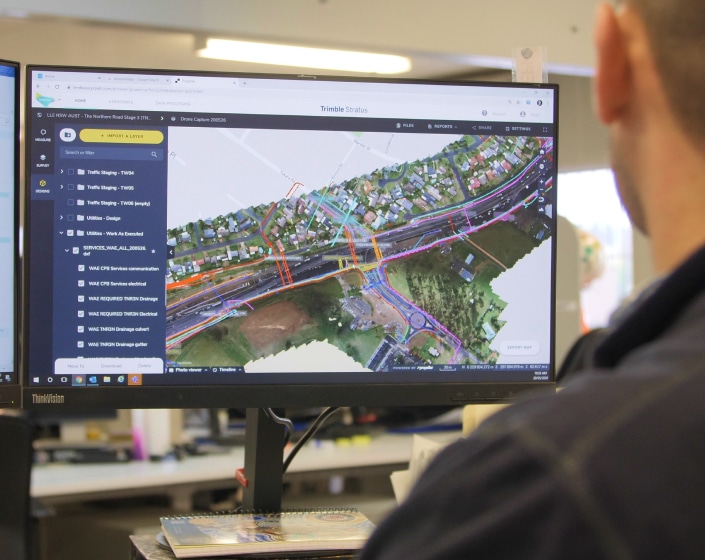
What is a digital twin?
A digital twin is a virtual representation of a physical object or process. This virtual model acts as a real-time digital counterpart to the physical object, using data collected by sensors, drones, robots, and other technology. The digital twin is then used to create visualizations and glean valuable insights about a project’s performance—often before it ever happens in reality.
Product engineering teams have used 3D renderings and computer-aided design (CAD) software for decades to validate product viability, simulate performance, and collect measurements. NASA famously created an early version of a digital twin back in 1970 to predict possible outcomes for the Apollo 13 mission.
According to IBM’s definition, “A digital twin is updated from real-time data and uses simulation, machine learning, and reasoning to help decision-making.” Which means that digital twins aren’t merely copies—they’re used to predict the future and make decisions based on those predictions.
Imagine a computer model of your car that reflects relevant data in real-time: how much gas you have in the tank, your tire pressure, when you’re due for an oil change, etc. With the right sensors, a computer could analyze the status of different engine components and predict potential trouble, so you could get your car serviced before there’s an issue.
Now imagine the impact this kind of technology could have on your worksites.
Building Information Modeling (BIM) technology already provides some of these benefits, but digital twins are actually connected to an object in the physical world through what’s called a “digital thread.” They aren’t theoretical—they’re accurate reflections of reality.
These digital duplicates help project teams better understand, optimize, and predict project outcomes.
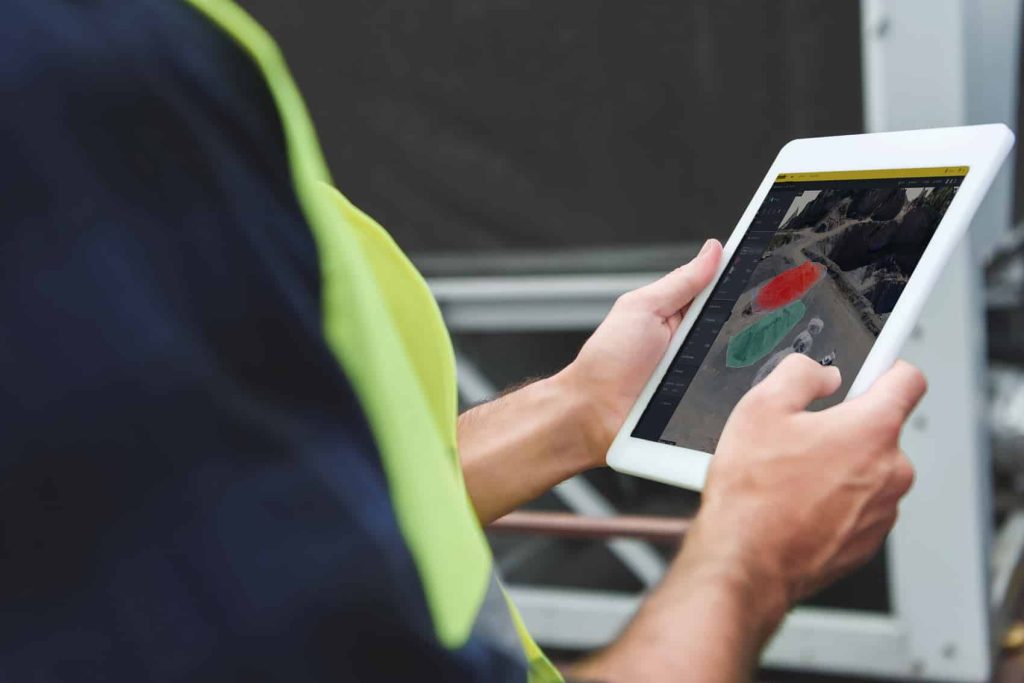
How digital twins are changing the face of construction
Construction has historically been a time- and labor-intensive process. We analyze design briefs, models, and linework in detail before a project even moves into production. Dozens of stakeholders are involved in every step.
Digital twins can help accelerate every stage of a project, from design through production and operations. Because these digital models really are “twins” of their real-world counterparts, they can accurately predict how a worksite will behave over time, or how it will respond to different conditions or processes.
Take Deakin University’s work on shoreline degradation as an example. With the proper data collection methods, we can create predictive simulations to show how Australia’s beaches will look in the future, or how they’ll respond to changing temperatures or weather patterns.
And the reach of this technology extends far beyond what we can physically measure. These computerized models can incorporate all kinds of data, including operational, financial, and social data to create a comprehensive understanding of a project from every angle.
What benefits can construction firms hope to gain from digital twins?
- Minimize risk: The ability to test solutions in a digital space helps identify, predict, and ultimately minimize risk. This includes hard risks like physical safety, as well as operational risks like cost overrun.
- Empower project teams: Creating a digital replica of a real-world environment before taking real-world action increases the likelihood of a project running smoothly. With data collected by drones and other equipment, digital twins can help project teams streamline efficiency, improve quality, and make better decisions.
- Improve decision-making: More and higher-quality data means better day-to-day decisions on site.
- Reduce costs: Despite the initial investment in technology, digital twins also can reduce overall construction costs by making it easier for projects to stay on budget and avoid costly mistakes.
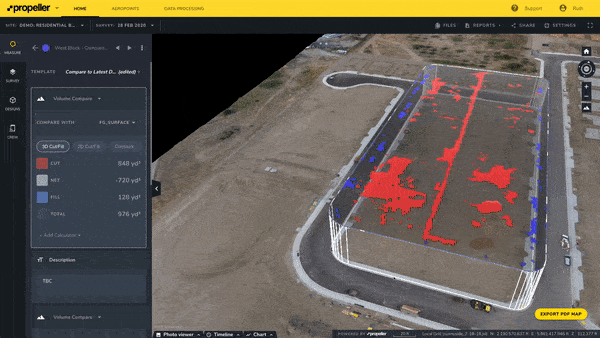
How to use 3D models to transform your next project
There are approximately 372,000 commercial drone operators in the U.S. alone, and many of these drone surveys are being used to create 3D models of worksites. These site models use the science of photogrammetry to create a hyper-accurate reflection of a worksite, complete with every angle, feature, and safety hazard.
In other words, 3D drone models are a type of digital twin when you fly a site frequently.
Using Propeller PPK, our customers can measure stockpile volumes, identify safety hazards, compare completed work against design, and track project efficiency—and that’s just the tip of the iceberg.
Check out this post for tips on how to make your site models as accurate as possible.