Post-processing kinematic (PPK) and real-time kinematic (RTK) workflows are only getting more accessible as new drone technology hits the market. But there’s still a lot of confusion about what this technology is, how it works, and what’s best for your surveying needs.
To cut through the complexity, we’re explaining how PPK workflows differ from RTK drone surveying, and where ground control fits in.
Ground control and traditional drone surveying
In traditional drone surveying, you need a sufficient number of known points to verify and pin your drone imagery to the ground.
Standard drones without GPS correctional processing are simply a vehicle for the camera. Their position in the sky is not accurately geotagged, so you don’t get reliable positional data from the drone hardware alone.
That level of accuracy comes from ground control, which is why even small errors in ground control setup can have enormous repercussions.
Ground control points (GCPs) can be known points marked and measured with a base and rover, or moveable, smart ground control points like Propeller’s AeroPoints.
Using GCPs when surveying is one way to ensure survey-grade accuracy, but setting them up is time-consuming on a large site—especially if you need to move them over time.
Setting up ground control with AeroPoints
If you’re working with smart GCPs like AeroPoints, you still need to place the hardware in an optimal distribution across the entire surveyed area. Yes, there’s still time and methodology involved in placement, but the time savings over shooting points on foot with a rover (and then painting them for visibility) is significant.
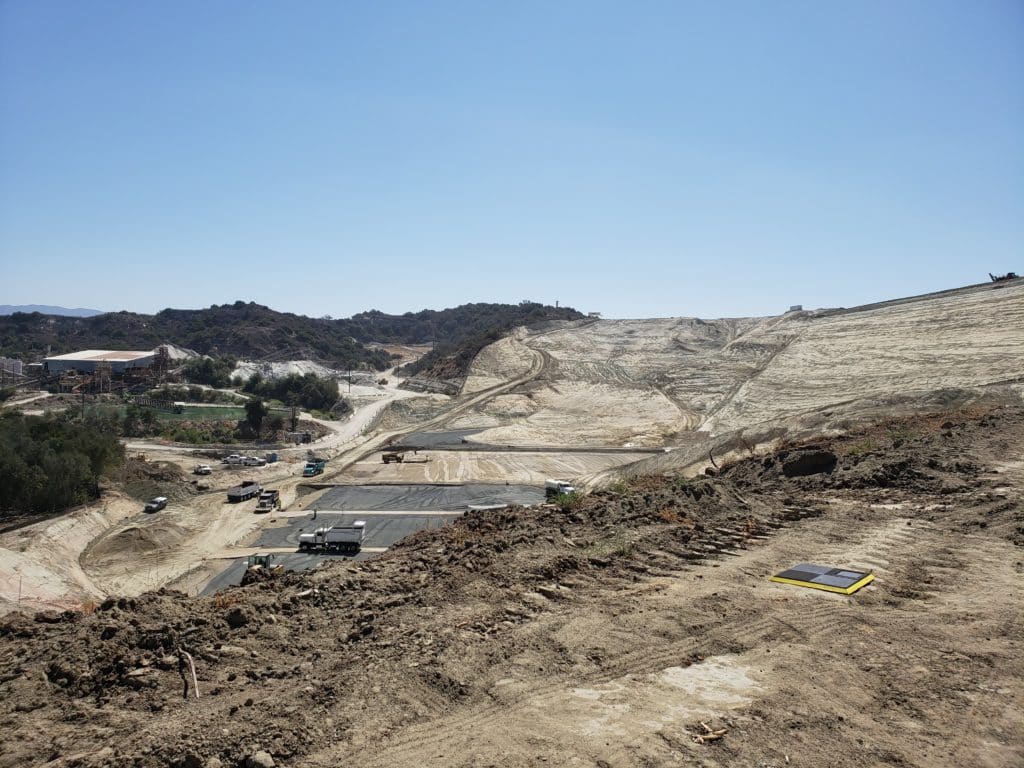
Once AeroPoints are in place, the process becomes even simpler. Press a single button to activate, and you’re done! They’re ready to start gathering information. When your drone survey is complete, just gather them back up. The AeroPoints will automatically search for a WiFi signal to begin uploading their data to the Propeller platform.
As recently as a few years ago, the planning, risk assessment, and legwork associated with traditional ground control was a necessary sacrifice.
New technology like AeroPoints and RTK-enabled drones are changing the landscape of modern surveying to make it faster, safer, and more cost-effective.
Onboard differential GPS has reduced the need for ground control
RTK-enabled drones have the ability to track their own geolocations accurately—an ability that most commercial drones lack. Using a PPK workflow is the best method for topoing a site that modern drone technology can offer, for reasons we’ll explore below.
But first, let’s explain what makes these two technologies different.
How on-board RTK technology works
Real-time kinematic (RTK) processing on a drone records GPS information and geotags images as they’re captured during flight. The GPS location is recorded for the center of each image.
While the drone is in flight, an active base station on the ground sends it raw GPS data. The drone’s onboard GPS combines that data with its own observations to accurately determine its position relative to the base.
This process works well—usually.
The RTK drone must stay connected to the base station while it’s gathering data in order for the two-way communication to inform positioning.
Unfortunately, signal loss can occur for several reasons: during turns due to antenna orientation, flying behind obstructions, patchy or unreliable signal, etc. When that happens, data becomes unreliable while the drone tries to regain contact with the base station.
What is RTK on a drone?
RTK stands for real time kinematic processing, it is a GPS correction technology that provides real time GPS location when survey drones are capturing photos of a surveying site. Basically RTK is an advanced GPS technology that helps to increase the accuracy of drone surveying results. RTK technology has been used on job sites in construction, mining, and waste management for years but only recently has the technology been adapted to be used in conjunction with drone surveying.
In short RTK technology helps to correct inaccurate information captured during drone surveying. These improvements enable a much higher level of accuracy from drone surveying results which can also be gathered much more efficiently then through other surveying methods.
RTK for Drones
When it comes to drone surveying in particular, RTK technology has significantly improved the level of accuracy that can be expected. In the early days of drone surveying the largest concern with the technology was whether or not it could accurately survey large areas without a significant margin of error in the data that was delivered. RTK technology was an essential part of quelling those concerns and getting drone surveying to the place that it is today as a mainstay in the surveying programs of most construction and mining companies.
Without the improvements that RTK technology offered for drone surveying there is a very good chance that drone surveying would have come and gone as a small fad that did not significantly disrupt the surveying industry. Instead it led to drone surveying being the most efficient and more importantly the most accurate method of surveying available on the market today.
RTK GPS drones
RTK GPS drones are simply a more advanced form of drone surveying that delivers a higher degree of accuracy than could be achieved without the presence of RTK technology. The GPS technology that RTK uses mixed with other essential technologies for drone surveying like photogrammetry are able to improve the accuracy of drone surveying so that the data can be gathered much more quickly but can also match the accuracy of traditional surveying methods which have always been time consuming, but were typically preferred because of their higher levels of data accuracy.
What’s the difference between PPK and RTK
That’s where PPK comes in. Unlike RTK, PPK isn’t hardware—it’s an entirely different processing workflow using an RTK-enabled drone.
What is PPK?
PPK stands for “post-processing kinematic.” The difference between PPK and RTK workflows is how base station data is processed for correction and accuracy.
In a PPK workflow, the drone associates X, Y, and Z coordinates with each image based on its onboard GPS unit. While this is happening, a base unit (this could be a base station, an AeroPoint, or CORS network) also records positional information, but with much more accurate triangulation.
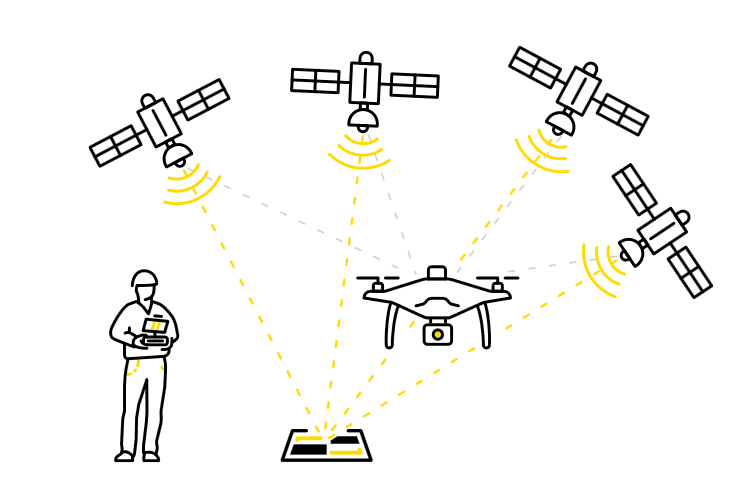
The two units work separately during flight, so there’s no need to maintain an active connection between the drone and the base to collect positional data accurate to 1/10 ft.
After the flight is over, the two sets of GPS data are matched together using image timestamps. The drone’s onboard GPS data is corrected by the more accurate base unit, providing precise geotags for image data after the fact.
While “real-time” technologies are appropriate in some situations, post-processing flight data using a PPK workflow adds an additional layer of reliability to surveys.