According to data gathered by KPMG, only a third of construction projects finish within 10% of their forecasted budgets. Even fewer finish within 10% of their projected completion date.
The impact of inefficiency has a very real cost:
- Nearly 35% of onsite work time is wasted on unproductive tasks
- Rework and other inefficiencies cost billions each year
- A boost in productivity could save the industry $1.6 trillion per year
These figures inspired us to share some ideas on the best ways to make worksites more productive and efficient. Even marginal gains in your operations, like reducing cycle times by one minute, can save thousands of dollars.
Here are three key strategies to improve worksite efficiency and productivity.
#1: Reduce downtime
Remember the statistic that 35% of onsite work time is wasted? Downtime is a significant contributor to this number. Waiting for other crews to finish, waiting for decisions to be made, and waiting for rework to be completed are all contributors to downtime
Construction and earthworks companies must be strategic about where and when they send their workers and their equipment—especially when resources are already limited.
Pausing to take a bird’s eye view of your worksite can help to minimize downtime. It’s easy to get lost in the details, but project managers and supervisors need to keep the big picture top of mind in order to accurately estimate the time and work remaining on a project and remain on schedule.
- Collect data regularly: If you know how to use it, frequent data collection through drone surveys can go a long way toward minimizing or even preventing downtime and increasing your worksite efficiency. Propeller PPK makes it easy to fly your site regularly and create detailed 3D maps complete with volume measurements. DirtMate fills in the gaps with near-instant field data: where equipment is located, which machines are operating, and where—along with field elevations for accurate survey data along traffic routes.
- Minimize change orders: Work is often paused while change orders are negotiated or adjustments are made to the project plan. Many of these changes can be prevented, though; accurate pre-bid topos and regular site surveys keep all stakeholders informed every step of the way to prevent miscommunication or mistakes based on bad data.
- Send teams where they’re needed: Daily and weekly survey data makes it easy to correctly position workers. If a subcontractor is still working or equipment is in the wrong place, waiting on replacements can cost thousands of dollars. You might even have to send a team home if they can’t access the site to complete their work. One Propeller customer estimates the total cost of downtime at around $3,500 per day—it all adds up quickly.
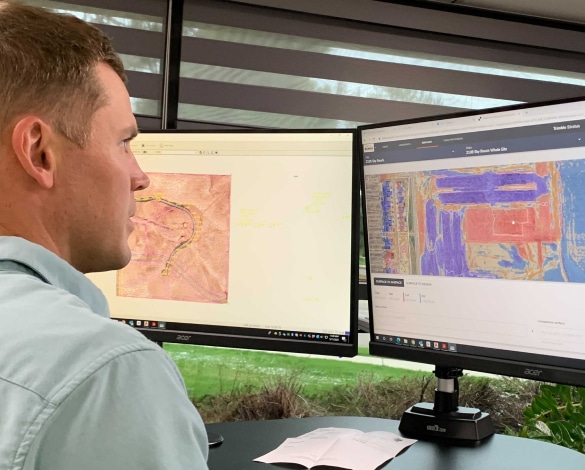
#2: Leverage tech
Today’s construction firms increasingly rely on cutting-edge technology to stay competitive. Tech has numerous benefits: increased accuracy, improved communication and access, safer worksites, and—of course—more efficient operations.
Technology can boost your worksite efficiency by:
- Automating manual tasks: There’s a reason why traditional base-and-rover surveys aren’t conducted very often. They’re expensive, time-consuming, and—depending on the site—dangerous. Once you’ve captured your data, you then need an expert with expensive CAD software to help interpret it for you. Drone surveying and other high-tech workflows make collecting and reviewing worksite data a simple process. Surveying a site becomes as easy as a 10-minute drone flight, and with Propeller, the data processing is completed in about 24 hours.
- Streamlining collaboration: When all project stakeholders have access to up-to-date site data and progress tracking, it’s much easier to collaborate. No one has to fill in the gaps with assumptions that can turn out to be a problem down the line. Cloud-based software like Propeller allows for field and office access to data for everyone who needs it.
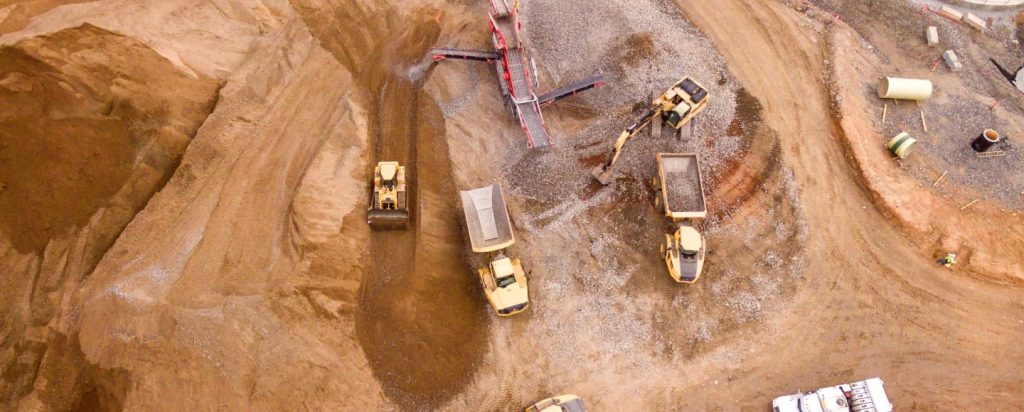
#3: Measure twice, move earth once
A balanced worksite is the ultimate goal. If your cut and fill are roughly equal, you’ll save time, money, and headache by not having to move it very far. But if your project requires you to move a lot of earth, you can only afford to move it once. Miscalculating your cut/fill can compromise your budget AND extend your project timeline with rework.
- Conduct accurate pre-bid surveys: An accurate bid may not help you undercut the competition, but it will protect your business and your bottom line. When you know exactly how much equipment and labor an earthwork project requires, you can submit an accurate bid.
- Measure again at takeoff: Takeoff surveys are just as important, since conditions may have changed since your pre-bid survey. Measuring twice at the start of a project will help prevent disputes, delays, and rework down the line.